Combining a range of geotechnical products, environmental innovation and global expertise, Keller is helping create a new future for Norway’s leading cancer hospital.
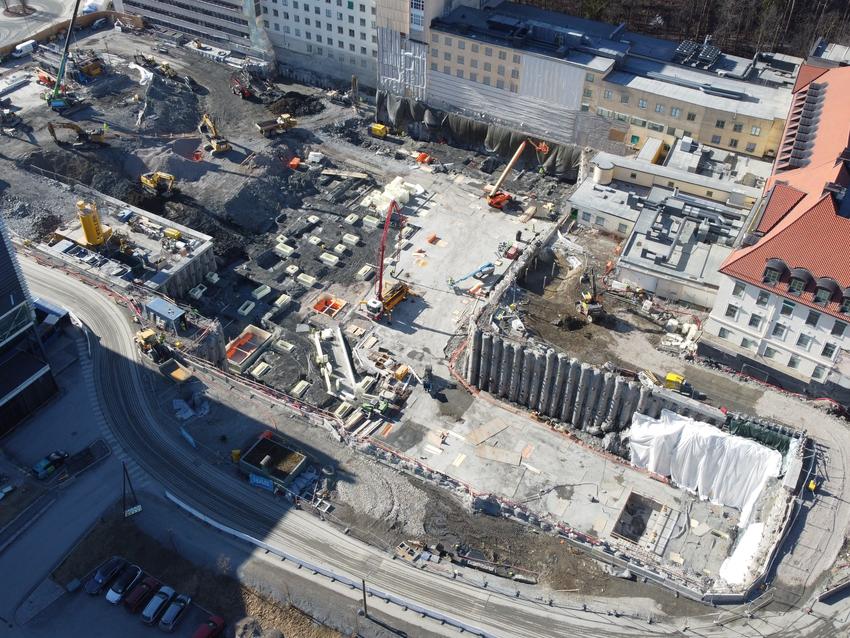
The Radiumhospitalet in Oslo is Norway’s main centre for cancer treatment and research. Founded in the 1930s, the hospital’s currently undergoing a major transformation, replacing outdated buildings with a state-of-the-art clinic and proton treatment centre.
It’s a complex project. The new buildings will be right in the heart of the campus, linked to existing buildings, while the foundations need to be constructed in soft clays and, in some areas, low-headroom conditions.
With the largest portfolio of geotechnical products in Norway, Keller was chosen by general contractor HAB Construction to join them in tendering for the project. During a competitive pitch, the team’s impressive initial proposal for a standard excavation pit with sheet piles and deep-soil mixing, was chosen as the strong favourite by the Government.
A greener solution
“Not only was the Government looking for a quality solution, but also one that considered the environment,” explains Dominik Gächter, Regional Manager. “We proposed using a silent piler for the sheet piles and a back-flow treatment plant for jet grouting. The plant filters the water in the spoil, which can then be reused, reducing the amount of spoil sent to landfill. This was one of the main reasons why we won the project.”
However, the proposal soon had to change. The building developer’s designer, having run into problems with settlement, cost and delays on a similar project on the same site, wanted what they perceived to be a less-risky solution.
Drawing on its expertise of different techniques and knowledge of the Norwegian clays, Keller quickly redesigned the project – switching from sheet piles to bored piles with a jet grout seal and fewer anchors, reducing the risk of water ingress and settlement.
Mind your head
The crew, using local experts, as well as those from Sweden and Austria, is installing 200 bored piles with 1200mm diameters, supported by 10,200m of anchors. To avoid the risk of large overconsumption of the concrete caused by the soft clays, the team has pre-stabilised the ground using deep soil mixing. The same technique is being used throughout the pit to provide a firm working platform.
With one area of the hospital to be built directly on bedrock, the team has also used a rock injection method to ensure water tightness. In another area of the site, jet grouting columns have been constructed in the cellar of an adjacent building, with headroom of less than 2m. “This presented a huge challenge – not just because of the amount of back flow coming out of the cellar, but also because it was below where MRI scans take place. This meant there were only limited hours we could work,” says Dominik.
Keeping the noise down
Working on a live hospital site has proved challenging and noise reduction is a key priority. One way Keller has mitigated this problem is through the use of reverse circulation drilling for both the anchors and the installation of 6,500m of steel core piles for the building foundations. This method involves water-powered rather than air-powered machinery, which is not only quieter, but also reduces vibration and the risk of settlement.
Throughout the project, Keller has worked quickly and flexibly, switching between techniques to avoid delays. In fact, despite a three-month delay at the start of the project – and the logistical headaches caused by COVID in terms of steel deliveries and bringing in crew from other areas of Europe – the project is running smoothly and is scheduled to finish on the original end date.
“This is a significant project for Keller in Norway,” says Dominik. “For us to be able to design a complete solution that reduces risk, noise and waste, and work in difficult areas, shows the market what we’re capable of. HAB and the end client are very happy and we now have more hospital project work lined up with the developer.”